Viime vuosina laserhitsaus on uuden energiateollisuuden nopean kehityksen ansiosta tunkeutunut nopeasti koko uudelle energiateollisuudelle nopeiden ja vakaiden etujensa ansiosta. Niistä laserhitsauslaitteet muodostavat suurimman osan sovelluksista koko uudella energiateollisuudella.
Laserhitsauson nopeasti tullut ykkösvalinta kaikilla elämänaloilla nopean nopeuden, suuren syvyyden ja pienten muodonmuutosten ansiosta. Pistehitseistä päittäishitseihin, muodostus- ja tiivistyshitseihin,laserhitsaustarjoaa vertaansa vailla olevan tarkkuuden ja hallinnan. Sillä on tärkeä rooli teollisessa tuotannossa ja valmistuksessa, mukaan lukien sotilasteollisuus, sairaanhoito, ilmailu, 3C-autoosat, mekaaniset levyt, uusi energia ja muut teollisuudenalat.
Verrattuna muihin hitsaustekniikoihin laserhitsauksella on ainutlaatuiset edut ja haitat.
Etu:
1. Nopea nopeus, suuri syvyys ja pieni muodonmuutos.
2. Hitsaus voidaan suorittaa normaalissa lämpötilassa tai erityisolosuhteissa, ja hitsauslaitteet ovat yksinkertaisia. Esimerkiksi lasersäde ei ajaudu sähkömagneettisessa kentässä. Laserit voivat hitsata tyhjiössä, ilmassa tai tietyissä kaasuympäristöissä, ja ne voivat hitsata materiaaleja, jotka ovat lasin läpi tai läpinäkyviä lasersäteelle.
3. Se voi hitsata tulenkestäviä materiaaleja, kuten titaania ja kvartsia, ja voi myös hitsata erilaisia materiaaleja hyvillä tuloksilla.
4. Kun laser on tarkennettu, tehotiheys on korkea. Kuvasuhde voi olla 5:1 ja jopa 10:1 hitsattaessa suuritehoisia laitteita.
5. Mikrohitsaus voidaan suorittaa. Kun lasersäde on tarkennettu, voidaan saada pieni piste ja se voidaan sijoittaa tarkasti. Sitä voidaan soveltaa mikro- ja pienten työkappaleiden kokoonpanoon ja hitsaukseen automatisoidun massatuotannon saavuttamiseksi.
6. Se voi hitsata vaikeapääsyisiä alueita ja suorittaa kosketuksetonta pitkän matkan hitsausta erittäin joustavasti. Erityisesti viime vuosina YAG-laserkäsittelytekniikka on ottanut käyttöön optisen kuidun siirtotekniikan, mikä on mahdollistanut laserhitsaustekniikan laajemman edistämisen ja soveltamisen.
7. Lasersäde on helppo jakaa ajassa ja tilassa, ja useita säteitä voidaan käsitellä useissa paikoissa samanaikaisesti, mikä luo edellytykset tarkempaan hitsaukseen.
Vika:
1. Työkappaleen kokoamistarkkuuden on oltava korkea, eikä palkin asentoa työkappaleessa saa merkittävästi poiketa. Tämä johtuu siitä, että laserpisteen koko tarkennuksen jälkeen on pieni ja hitsisauma on kapea, mikä vaikeuttaa täytemetallimateriaalien lisäämistä. Jos työkappaleen kokoamistarkkuus tai palkin asennon tarkkuus ei täytä vaatimuksia, hitsausvirheitä voi esiintyä.
2. Laserien ja niihin liittyvien järjestelmien kustannukset ovat korkeat, ja kertainvestointi on suuri.
Yleisiä laserhitsausvirheitälitiumakkujen valmistuksessa
1. Hitsauksen huokoisuus
Yleisiä puutteitalaserhitsausovat huokoset. Hitsaussula on syvä ja kapea. Laserhitsausprosessin aikana typpi tunkeutuu sulaan altaaseen ulkopuolelta. Metallin jäähtymis- ja jähmettymisprosessin aikana typen liukoisuus heikkenee lämpötilan laskiessa. Kun sula altaan metalli jäähtyy ja alkaa kiteytyä, liukoisuus laskee jyrkästi ja äkillisesti. Tällä hetkellä suuri määrä kaasua saostuu muodostaen kuplia. Jos kuplien kellumisnopeus on pienempi kuin metallin kiteytymisnopeus, syntyy huokosia.
Litiumparistoteollisuuden sovelluksissa havaitsemme usein, että huokoset ovat erityisen todennäköisiä positiivisen elektrodin hitsauksen aikana, mutta niitä esiintyy harvoin negatiivisen elektrodin hitsauksen aikana. Tämä johtuu siitä, että positiivinen elektrodi on valmistettu alumiinista ja negatiivinen elektrodi on valmistettu kuparista. Hitsauksen aikana pinnalla oleva nestemäinen alumiini on tiivistynyt ennen kuin sisäinen kaasu on vuotanut kokonaan yli, mikä estää kaasua vuotamasta yli ja muodostamasta suuria ja pieniä reikiä. Pieni stomata.
Edellä mainittujen huokosten syiden lisäksi huokosiin kuuluvat myös ulkoilma, kosteus, pintaöljy jne. Lisäksi typen puhalluksen suunta ja kulma vaikuttavat myös huokosten muodostumiseen.
Entä kuinka vähentää hitsaushuokosten esiintymistä?
Ensin ennenhitsaus, öljytahrat ja epäpuhtaudet saapuvien materiaalien pinnalla on puhdistettava ajoissa; litiumakkujen tuotannossa saapuvan materiaalin tarkastus on olennainen prosessi.
Toiseksi suojakaasuvirtausta tulee säätää tekijöiden, kuten hitsausnopeuden, tehon, asennon jne. mukaan, eikä se saa olla liian suuri eikä liian pieni. Suojavaipan painetta tulee säätää tekijöiden, kuten laserin tehon ja tarkennuksen asennon mukaan, eikä se saa olla liian korkea tai liian matala. Suojavaippasuuttimen muoto tulee säätää hitsin muodon, suunnan ja muiden tekijöiden mukaan siten, että suojavaippa peittää tasaisesti hitsausalueen.
Kolmanneksi säädä ilman lämpötilaa, kosteutta ja pölyä työpajassa. Ympäristön lämpötila ja kosteus vaikuttavat alustan pinnan kosteuspitoisuuteen ja suojakaasuun, mikä puolestaan vaikuttaa vesihöyryn muodostumiseen ja poistumiseen sulassa altaassa. Jos ympäristön lämpötila ja kosteus ovat liian korkeat, alustan ja suojakaasun pinnalle on liikaa kosteutta, jolloin muodostuu suuri määrä vesihöyryä, mikä johtaa huokosiin. Jos ympäristön lämpötila ja kosteus ovat liian alhaiset, alustan pinnalla ja suojakaasussa on liian vähän kosteutta, mikä vähentää vesihöyryn muodostumista ja siten huokosia; anna laatuhenkilöstön havaita lämpötilan, kosteuden ja pölyn tavoitearvo hitsausasemalla.
Neljänneksi säteen heilahdusmenetelmää käytetään vähentämään tai poistamaan huokoset lasersyväläpihitsauksessa. Hitsauksen aikana tapahtuvan heilahtelun vuoksi palkin edestakainen heilautus hitsaussaumaan aiheuttaa osan hitsaussaumasta toistuvan uudelleensulatuksen, mikä pidentää nestemäisen metallin viipymisaikaa hitsausaltaassa. Samalla palkin taipuma lisää myös lämmöntuottoa pinta-alayksikköä kohti. Hitsin syvyys-leveyssuhde pienenee, mikä edistää kuplien syntymistä, mikä eliminoi huokoset. Toisaalta palkin heilahdus saa pienen reiän heilumaan vastaavasti, mikä voi myös tarjota sekoitusvoimaa hitsausaltaalle, lisätä hitsausaltaan konvektiota ja sekoittumista sekä vaikuttaa suotuisasti huokosten poistamiseen.
Viidenneksi pulssitaajuus, pulssitaajuus viittaa lasersäteen lähettämien pulssien määrään aikayksikköä kohti, mikä vaikuttaa lämmön syöttöön ja lämmön kertymiseen sulassa altaassa ja sitten lämpötila- ja virtauskenttään sulassa. uima-allas. Jos pulssitaajuus on liian korkea, se johtaa liialliseen lämmön syöttöön sulaan altaan, mikä saa sulan altaan lämpötilan olemaan liian korkea, jolloin syntyy metallihöyryä tai muita elementtejä, jotka ovat haihtuvia korkeissa lämpötiloissa, mikä johtaa huokosiin. Jos pulssitaajuus on liian alhainen, se johtaa riittämättömään lämmön kertymiseen sulaan altaan, jolloin sulan lämpötila laskee liian alhaiseksi, mikä vähentää kaasun liukenemista ja karkaamista, mikä johtaa huokosiin. Yleisesti ottaen pulssitaajuus tulee valita kohtuulliselta alueelta substraatin paksuuden ja lasertehon perusteella, ja vältä liian korkeaa tai liian matalaa.
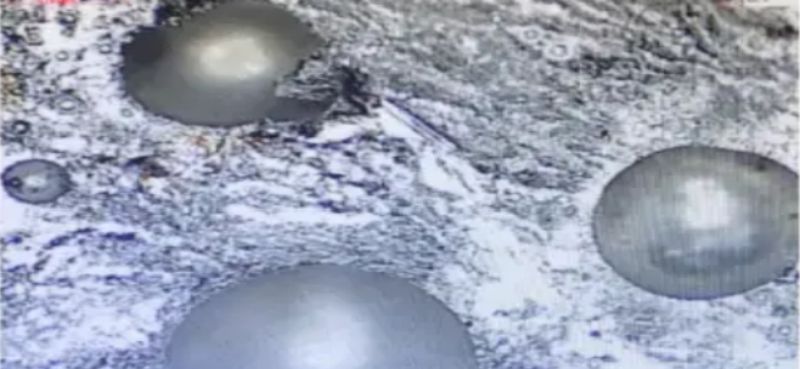
Hitsausreiät (laserhitsaus)
2. Hitsausroiskeet
Hitsausprosessin, laserhitsauksen aikana syntyvä roiske vaikuttaa vakavasti hitsin pinnan laatuun ja saastuttaa ja vahingoittaa linssiä. Yleinen suorituskyky on seuraava: laserhitsauksen päätyttyä materiaalin tai työkappaleen pinnalle ilmaantuu monia metallihiukkasia, jotka tarttuvat materiaalin tai työkappaleen pintaan. Intuitiivisin suorituskyky on se, että galvanometrin tilassa hitsattaessa galvanometrin suojalinssin käytön jälkeen pinnalle tulee tiheitä kuoppia, jotka johtuvat hitsausroiskeista. Pitkän ajan kuluttua valo on helppo estää, ja hitsausvalon kanssa tulee ongelmia, mikä johtaa sarjaan ongelmia, kuten hitsauksen katkeaminen ja virtuaalinen hitsaus.
Mitkä ovat roiskumisen syyt?
Ensinnäkin tehotiheys, mitä suurempi tehotiheys, sitä helpompi on tuottaa roiskeita, ja roiske liittyy suoraan tehotiheyteen. Tämä on vuosisadan vanha ongelma. Teollisuus ei ainakaan toistaiseksi ole kyennyt ratkaisemaan roiskumisongelmaa, ja voi vain sanoa, että se on hieman vähentynyt. Litiumakkuteollisuudessa roiskuminen on suurin syyllinen akun oikosulkuun, mutta se ei ole pystynyt ratkaisemaan perimmäistä syytä. Roiskeiden vaikutusta akkuun voidaan vähentää vain suojauksen kannalta. Esimerkiksi hitsausosan ympärille on lisätty ympyrä pölynpoistoaukkoja ja suojakansia, ja ilmateriä on lisätty ympyröissä estämään roiskeita tai jopa akun vaurioitumista. Hitsausaseman ympäristön, tuotteiden ja komponenttien tuhoamisen voidaan sanoa käyttäneen keinot loppuun.
Mitä tulee roiskeongelman ratkaisemiseen, voidaan vain sanoa, että hitsausenergian vähentäminen auttaa vähentämään roiskeita. Hitsausnopeuden alentaminen voi myös auttaa, jos tunkeuma ei ole riittävä. Mutta joissakin erityisissä prosessivaatimuksissa sillä on vain vähän vaikutusta. Se on sama prosessi, eri koneilla ja eri materiaalierillä on täysin erilaiset hitsausvaikutukset. Siksi uudessa energiateollisuudessa on kirjoittamaton sääntö, yksi hitsausparametrisarja yhdelle laitteelle.
Toiseksi, jos käsitellyn materiaalin tai työkappaleen pintaa ei puhdisteta, myös öljytahrat tai epäpuhtaudet aiheuttavat vakavia roiskeita. Tällä hetkellä helpoin asia on puhdistaa käsitellyn materiaalin pinta.
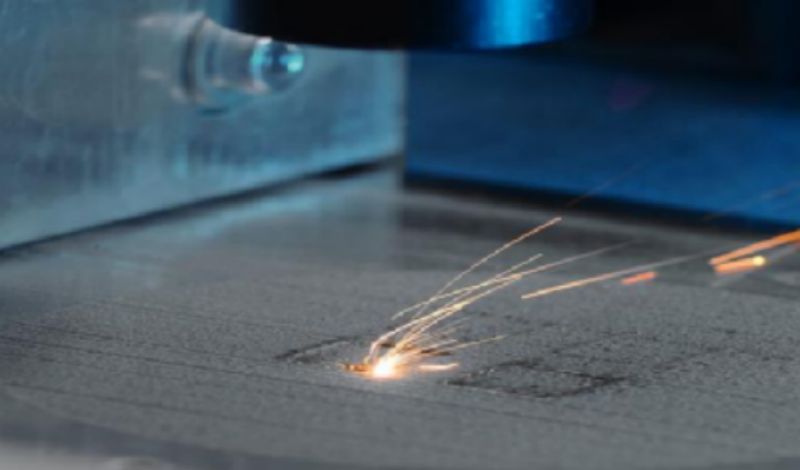
3. Laserhitsauksen korkea heijastavuus
Yleisesti ottaen korkea heijastus viittaa siihen, että prosessointimateriaalilla on pieni resistiivisyys, suhteellisen sileä pinta ja alhainen absorptionopeus lähi-infrapunalasereilla, mikä johtaa suureen määrään laseremissiota ja koska useimpia lasereita käytetään pystysuorassa Materiaalin tai pienen kallistuksen vuoksi palaava laservalo palaa lähtöpäähän ja jopa osa palaavasta valosta kytkeytyy energiaa välittävään kuituun ja siirtyy takaisin kuitua pitkin sisäpuolelle laserin, jolloin laserin sisällä olevat ydinkomponentit ovat edelleen korkeassa lämpötilassa.
Kun heijastuskyky on liian korkea laserhitsauksen aikana, voidaan tehdä seuraavat ratkaisut:
3.1 Käytä heijastuksenestopinnoitetta tai käsittele materiaalin pinta: hitsausmateriaalin pinnan pinnoittaminen heijastuksenestopinnoitteella voi vähentää tehokkaasti laserin heijastavuutta. Tämä pinnoite on yleensä erityinen optinen materiaali, jolla on alhainen heijastavuus ja joka absorboi laserenergiaa sen sijaan, että se heijastaisi sitä takaisin. Joissakin prosesseissa, kuten virtakollektorihitsauksessa, pehmeässä liitoksessa jne., pinta voidaan myös kohokuvioida.
3.2 Hitsauskulman säätäminen: Hitsauskulmaa säätämällä lasersäde voi osua hitsausmateriaaliin sopivammassa kulmassa ja vähentää heijastuksen esiintymistä. Normaalisti lasersäteen osuminen kohtisuoraan hitsattavan materiaalin pintaan on hyvä tapa vähentää heijastuksia.
3.3 Apuimuaineen lisääminen: Hitsauksen aikana hitsaukseen lisätään tietty määrä apuimuainetta, kuten jauhetta tai nestettä. Nämä absorboijat absorboivat laserenergiaa ja vähentävät heijastavuutta. Sopiva imuaine on valittava erityisten hitsausmateriaalien ja käyttöskenaarioiden perusteella. Litiumparistoteollisuudessa tämä on epätodennäköistä.
3.4 Käytä optista kuitua laserin lähettämiseen: Jos mahdollista, optista kuitua voidaan käyttää laserin siirtämiseen hitsausasentoon heijastavuuden vähentämiseksi. Optiset kuidut voivat ohjata lasersäteen hitsausalueelle, jotta vältetään suora altistuminen hitsausmateriaalin pinnalle ja vähennetään heijastusten esiintymistä.
3.5 Laserparametrien säätäminen: Säätämällä parametreja, kuten laserin tehoa, polttoväliä ja polttohalkaisijaa, voidaan ohjata laserenergian jakautumista ja vähentää heijastuksia. Joillekin heijastaville materiaaleille lasertehon vähentäminen voi olla tehokas tapa vähentää heijastuksia.
3.6 Käytä säteenjakajaa: Säteenjakaja voi ohjata osan laserenergiasta absorptiolaitteeseen, mikä vähentää heijastusten esiintymistä. Säteenjakolaitteet koostuvat yleensä optisista komponenteista ja vaimentimista, ja valitsemalla sopivat komponentit ja säätämällä laitteen sijoittelua voidaan saavuttaa pienempi heijastuskyky.
4. Hitsaus alaleikkaus
Mitkä prosessit aiheuttavat todennäköisemmin alittavuutta litiumakun valmistusprosessissa? Miksi alihinnoittelu tapahtuu? Analysoidaan se.
Alileikkaus, yleensä hitsausraaka-aineet eivät ole hyvin yhdistetty toisiinsa, rako on liian suuri tai ura tulee näkyviin, syvyys ja leveys ovat periaatteessa suurempia kuin 0,5 mm, kokonaispituus on yli 10 % hitsin pituudesta, tai suurempi kuin tuoteprosessistandardi vaadittu pituus.
Koko litiumakun valmistusprosessissa alileikkaus tapahtuu todennäköisemmin, ja se jakautuu yleensä sylinterimäisen kansilevyn tiivistyksen esihitsaukseen ja hitsaukseen sekä neliömäisen alumiinikuoren kansilevyn tiivistyksen esihitsaukseen ja hitsaukseen. Pääsyynä on se, että tiivisteen kansilevyn on toimittava yhteistyössä kuoren kanssa hitsausta varten, tiivistyspeitelevyn ja vaipan välinen sovitusprosessi on altis liiallisille hitsausrakoille, urille, luhistumiselle jne., joten se on erityisen altis alileikkauksille. .
Mikä siis aiheuttaa alittavuuden?
Jos hitsausnopeus on liian nopea, hitsin keskelle osoittavan pienen reiän takana oleva nestemäinen metalli ei ehdi jakautua uudelleen, mikä johtaa jähmettymiseen ja hitsin molemmille puolille alileikkaukseen. Yllä olevan tilanteen vuoksi meidän on optimoitava hitsausparametrit. Yksinkertaisesti sanottuna se on toistuvia kokeita eri parametrien tarkistamiseksi, ja DOE:tä jatketaan, kunnes sopivat parametrit on löydetty.
2. Hitsausmateriaalien liialliset hitsausraot, urat, painumat jne. vähentävät rakot täyttävän sulan metallin määrää, mikä tekee alileikkausten todennäköisyydestä. Tämä on laitteisto- ja raaka-ainekysymys. Täyttävätkö hitsausraaka-aineet prosessimme saapuvat materiaalivaatimukset, vastaako laitteiden tarkkuus vaatimuksia jne. Normaali käytäntö on jatkuvasti kiduttaa ja lyödä toimittajia ja laitteista vastaavia henkilöitä.
3. Jos energia putoaa liian nopeasti laserhitsauksen lopussa, pieni reikä voi painua kokoon, mikä johtaa paikalliseen alileikkaukseen. Tehon ja nopeuden oikea yhteensovittaminen voi tehokkaasti estää aliviivojen muodostumisen. Kuten vanha sanonta kuuluu, toista kokeita, tarkista eri parametrit ja jatka DOE:tä, kunnes löydät oikeat parametrit.
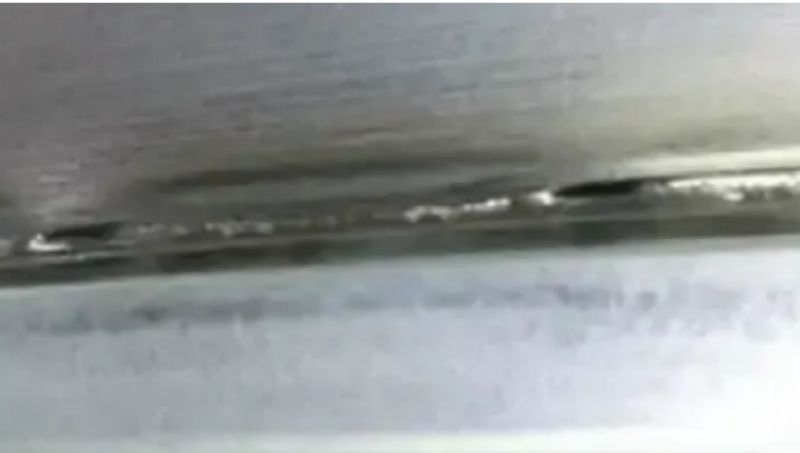
5. Hitsauskeskuksen romahdus
Jos hitsausnopeus on hidas, sulasta tulee suurempi ja leveämpi, mikä lisää sulan metallin määrää. Tämä voi vaikeuttaa pintajännityksen ylläpitämistä. Kun sula metalli tulee liian raskaaksi, hitsin keskikohta voi vajota ja muodostaa kuoppia ja kuoppia. Tässä tapauksessa energiatiheyttä on pienennettävä asianmukaisesti sulaaltaan romahtamisen estämiseksi.
Toisessa tilanteessa hitsausrako vain muodostaa painumisen aiheuttamatta rei'itystä. Tämä on epäilemättä laitteiden puristussovituksen ongelma.
Laserhitsauksen aikana mahdollisesti ilmenevien vikojen ja erilaisten vikojen syiden asianmukainen ymmärtäminen mahdollistaa kohdennetumman lähestymistavan mahdollisten epänormaalien hitsausongelmien ratkaisemiseen.
6. Hitsaushalkeamat
Jatkuvassa laserhitsauksessa ilmenevät halkeamat ovat pääasiassa lämpöhalkeamia, kuten kidehalkeamia ja nestemäisiä halkeamia. Näiden halkeamien pääasiallinen syy on hitsin synnyttämät suuret kutistumisvoimat ennen kuin se jähmettyy kokonaan.
Laserhitsauksen halkeamien syyt ovat myös seuraavat:
1. Kohtuuton hitsaussuunnittelu: Väärä hitsin geometrian ja koon suunnittelu voi aiheuttaa hitsausjännityksen keskittymistä, mikä aiheuttaa halkeamia. Ratkaisu on optimoida hitsin suunnittelu hitsausjännityksen keskittymisen välttämiseksi. Voit käyttää sopivia offset-hitsauksia, muuttaa hitsin muotoa jne.
2. Hitsausparametrien yhteensopimattomuus: Virheellinen hitsausparametrien valinta, kuten liian nopea hitsausnopeus, liian suuri teho jne., voi johtaa epätasaisiin lämpötilan muutoksiin hitsausalueella, mikä johtaa suuriin hitsausjännityksiin ja halkeamiin. Ratkaisu on säätää hitsausparametrit vastaamaan tiettyä materiaalia ja hitsausolosuhteita.
3. Hitsauspinnan huono esikäsittely: Hitsauspinnan asianmukaisen puhdistuksen ja esikäsittelyn laiminlyönti ennen hitsausta, kuten oksidien, rasvan jne. poistaminen, vaikuttaa hitsin laatuun ja lujuuteen ja aiheuttaa helposti halkeamia. Ratkaisu on puhdistaa ja esikäsitellä hitsauspinta riittävästi, jotta hitsausalueen epäpuhtaudet ja epäpuhtaudet käsitellään tehokkaasti.
4. Virheellinen hitsauslämmöntuodon säätö: Hitsauksen aikana tapahtuvan lämmöntuoton huono hallinta, kuten liiallinen lämpötila hitsauksen aikana, hitsauskerroksen väärä jäähdytysnopeus jne., johtaa muutoksiin hitsausalueen rakenteessa, mikä johtaa halkeamiin . Ratkaisu on säätää lämpötilaa ja jäähdytysnopeutta hitsauksen aikana ylikuumenemisen ja nopean jäähtymisen välttämiseksi.
5. Riittämätön jännityksenpoisto: Riittämätön jännityksenpoistokäsittely hitsauksen jälkeen johtaa riittämättömään jännityksenpoistoon hitsausalueella, mikä johtaa helposti halkeamiin. Ratkaisu on suorittaa sopiva jännityksenpoistokäsittely hitsauksen jälkeen, kuten lämpökäsittely tai tärinäkäsittely (pääsyy).
Mitä tulee litiumakkujen valmistusprosessiin, mitkä prosessit aiheuttavat todennäköisemmin halkeamia?
Yleensä halkeamia syntyy herkästi tiivistyshitsauksen aikana, kuten lieriömäisten teräskuorien tai alumiinikuorien tiivistyshitsauksessa, neliömäisten alumiinikuorien tiivistyshitsauksessa jne. Lisäksi moduulipakkausprosessin aikana myös virrankerääjän hitsaus on altis. halkeamiin.
Tietysti voimme käyttää myös täytelankaa, esilämmitystä tai muita menetelmiä näiden halkeamien vähentämiseksi tai poistamiseksi.
Postitusaika: 01.09.2023